Mrp Erp Meaning
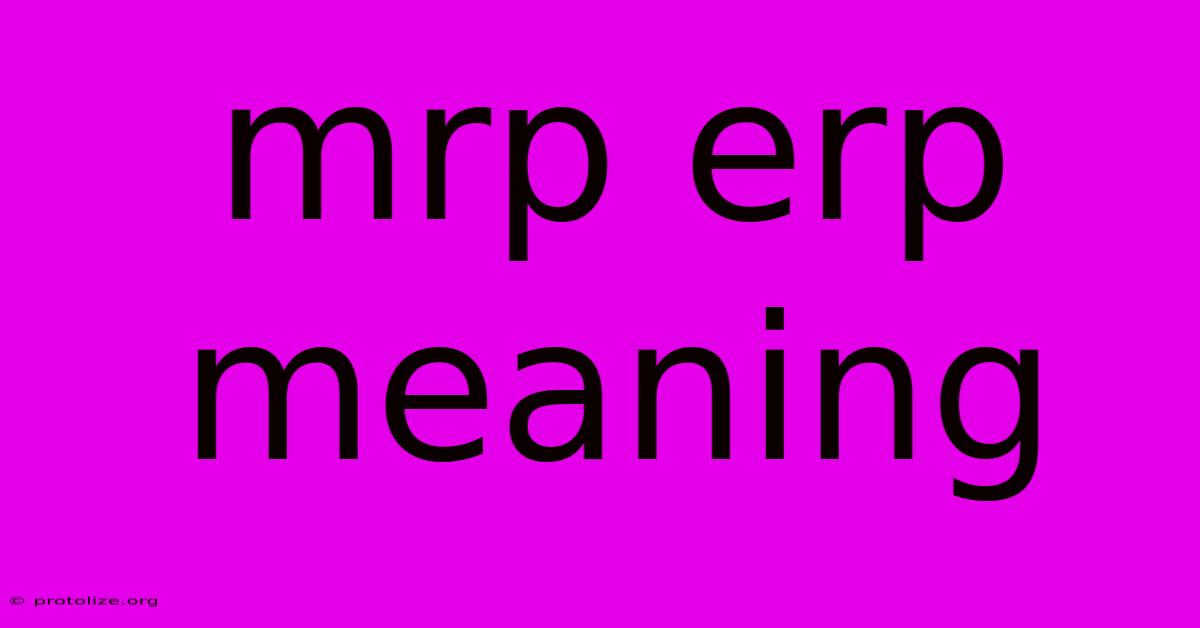
Discover more detailed and exciting information on our website. Click the link below to start your adventure: Visit Best Website mr.cleine.com. Don't miss out!
Table of Contents
MRP and ERP: Understanding the Core Differences and Synergies
For businesses looking to optimize their operations and gain a competitive edge, understanding the nuances of MRP (Material Requirements Planning) and ERP (Enterprise Resource Planning) is crucial. While often used interchangeably, these two systems serve distinct purposes, yet frequently work in tandem. This article will delve into the meaning of MRP and ERP, highlighting their individual functionalities and how they integrate to streamline business processes.
What is MRP? (Material Requirements Planning)
MRP, at its core, is a production planning and inventory control system. Its primary function is to determine the precise quantities of materials needed to meet production schedules. It achieves this by:
- Analyzing the Bill of Materials (BOM): The BOM lists all the raw materials, components, and sub-assemblies required to manufacture a product. MRP meticulously examines the BOM to determine the necessary quantities.
- Considering the Master Production Schedule (MPS): The MPS outlines the planned production volume for each product over a specific period. MRP uses this schedule to calculate material needs aligned with production deadlines.
- Accounting for Inventory Levels: MRP takes existing inventory levels into account to determine what materials need to be ordered or produced. This helps minimize waste and storage costs.
Key Benefits of MRP:
- Reduced Inventory Costs: By precisely planning material needs, MRP minimizes overstocking and reduces storage costs.
- Improved Production Scheduling: MRP ensures that the necessary materials are available when needed, preventing production delays.
- Enhanced Production Efficiency: With optimized material flow, production processes become more efficient.
- Better Demand Forecasting: Through analysis of historical data and production schedules, MRP helps predict future demand for materials.
However, MRP's scope is limited. It primarily focuses on production planning and inventory management within the manufacturing realm. It doesn't integrate with other crucial business functions such as finance, human resources, or sales. This is where ERP comes into play.
What is ERP? (Enterprise Resource Planning)
ERP is a broader, more integrated system designed to manage and integrate all facets of a business. It consolidates data from various departments into a central database, providing a unified view of the entire organization. Key ERP modules often include:
- Financial Management: Accounting, budgeting, and financial reporting.
- Human Resources Management: Payroll, benefits administration, and employee management.
- Supply Chain Management: Procurement, inventory management, and logistics. This is where MRP often integrates.
- Customer Relationship Management (CRM): Sales, marketing, and customer service.
- Manufacturing Management: Production planning, scheduling, and quality control. This often includes MRP functionality.
Key Benefits of ERP:
- Improved Data Visibility: Access to real-time data across all departments.
- Enhanced Collaboration: Improved communication and collaboration between departments.
- Streamlined Processes: Automation of manual tasks and optimization of workflows.
- Reduced Costs: Improved efficiency and reduced waste across the organization.
- Better Decision Making: Access to comprehensive data enables more informed decisions.
The Synergy Between MRP and ERP
While distinct, MRP and ERP often work together seamlessly. Within a larger ERP system, MRP functions as a key component within the supply chain management or manufacturing modules. This integration offers significant advantages:
- Real-time Inventory Visibility: ERP provides a centralized view of inventory levels, which is crucial for MRP's accurate calculations.
- Improved Demand Forecasting: ERP's data from sales and marketing can inform MRP's demand forecasting, resulting in more accurate material planning.
- Optimized Production Scheduling: The integration ensures that production schedules are aligned with available resources and materials.
- Reduced Lead Times: The streamlined flow of information reduces delays and optimizes lead times.
Choosing Between MRP and ERP: Which is Right for Your Business?
The choice between MRP and ERP depends heavily on your business size, complexity, and specific needs.
- Small Businesses with Simple Production: A standalone MRP system might suffice.
- Growing Businesses with Multiple Departments: An ERP system offers the scalability and integration necessary to support growth.
- Large Enterprises with Complex Operations: An integrated ERP system incorporating advanced MRP capabilities is essential.
In conclusion, understanding the distinct roles of MRP and ERP is crucial for effective business management. While MRP focuses on optimizing material requirements, ERP provides a holistic view and integrated management of all organizational aspects. The synergy between these systems enables businesses to improve efficiency, reduce costs, and gain a significant competitive advantage.
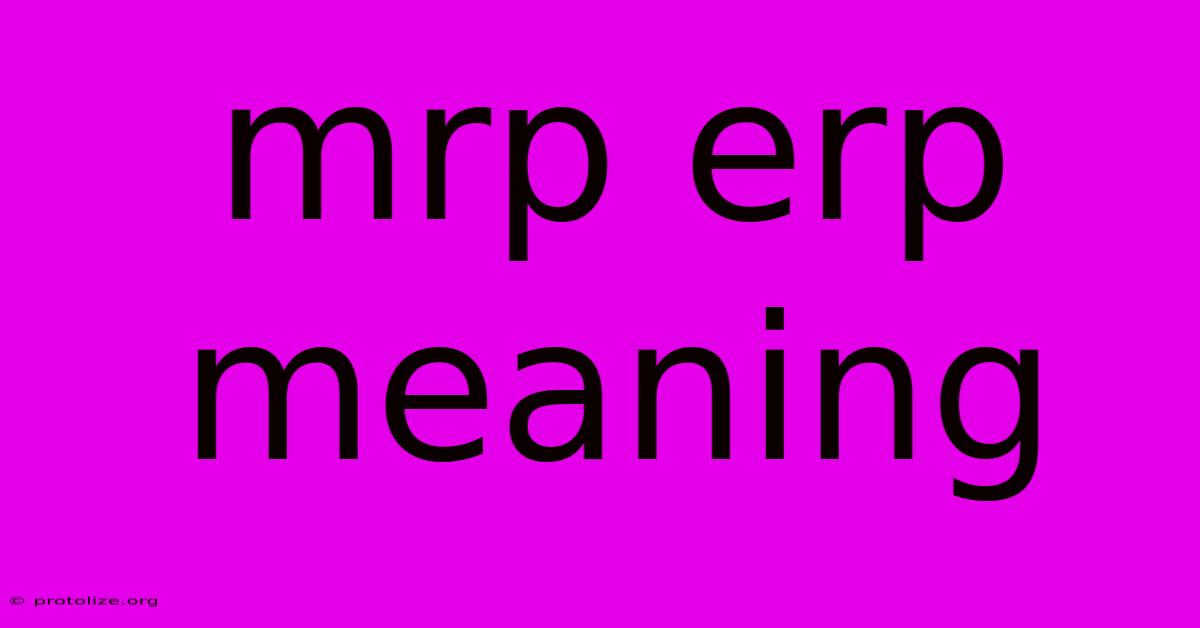
Thank you for visiting our website wich cover about Mrp Erp Meaning. We hope the information provided has been useful to you. Feel free to contact us if you have any questions or need further assistance. See you next time and dont miss to bookmark.
Featured Posts
-
Blizzard Snow Squall Hitting Parts Of Ontario
Dec 13, 2024
-
Open Ai Fixes Chat Gpt Service Disruption
Dec 13, 2024
-
Selena Gomez Engaged To Producer
Dec 13, 2024
-
Erp Zeal Login
Dec 13, 2024
-
Greenstar 25i Erp Condensing Combi Boiler
Dec 13, 2024