Erp Vs Plm
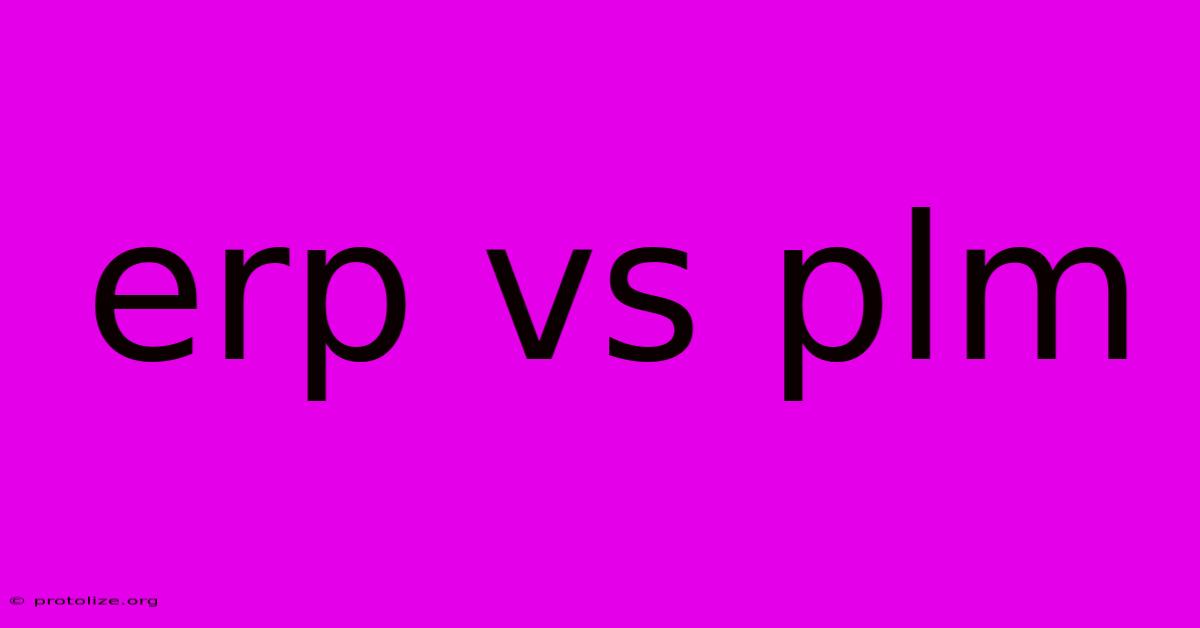
Discover more detailed and exciting information on our website. Click the link below to start your adventure: Visit Best Website mr.cleine.com. Don't miss out!
Table of Contents
ERP vs. PLM: Choosing the Right System for Your Business
Choosing the right software for your business can feel overwhelming. Two systems often considered are Enterprise Resource Planning (ERP) and Product Lifecycle Management (PLM). While they might seem similar at first glance, they serve distinct purposes and cater to different needs. This article will delve into the key differences between ERP and PLM, helping you determine whichβor if bothβare right for your organization.
Understanding ERP (Enterprise Resource Planning)
ERP systems are the backbone of many businesses, integrating various departments and functions into a single, unified system. Think of it as a central nervous system for your company. ERP software manages core business processes, including:
- Finance: Accounting, budgeting, financial reporting.
- Human Resources: Payroll, employee management, recruiting.
- Supply Chain Management: Procurement, inventory management, order fulfillment.
- Manufacturing: Production planning, scheduling, quality control.
- Customer Relationship Management (CRM): Sales, marketing, customer service (often integrated or a separate module).
Key benefits of ERP include:
- Improved efficiency: Streamlined processes and automated tasks lead to significant time savings.
- Enhanced visibility: Real-time data provides a clear overview of business operations.
- Better collaboration: Improved communication and data sharing between departments.
- Reduced costs: Optimized processes and reduced errors lead to cost savings.
- Data-driven decision-making: Access to accurate, real-time data empowers informed decisions.
Understanding PLM (Product Lifecycle Management)
PLM, on the other hand, focuses specifically on the entire lifecycle of a product, from initial concept to end-of-life. It's a critical system for companies that develop and manufacture products, managing the complex processes involved in bringing a product to market. PLM software handles:
- Product design and development: CAD data management, collaboration tools, simulation, and analysis.
- Manufacturing process planning: Bill of materials (BOM) management, process optimization, and production scheduling.
- Supply chain management (specific to product development): Sourcing materials, managing suppliers, and ensuring quality control.
- Product data management: Centralized repository for all product-related information, including drawings, specifications, and documentation.
- Compliance and regulatory management: Tracking and managing compliance with industry regulations.
Key benefits of PLM include:
- Improved product quality: Enhanced collaboration and better control over the product development process.
- Faster time-to-market: Streamlined workflows and efficient data management accelerate product development.
- Reduced development costs: Improved collaboration and reduced errors lead to cost savings.
- Enhanced innovation: Easier collaboration fosters creativity and facilitates the development of innovative products.
- Better product traceability: Complete history of product development, manufacturing, and usage.
ERP vs. PLM: Key Differences Summarized
Feature | ERP | PLM |
---|---|---|
Focus | Overall business processes | Product lifecycle management |
Scope | Broader, encompassing many departments | Narrower, focused on product development |
Key users | Finance, HR, supply chain, manufacturing | Engineering, design, manufacturing, supply chain (product-focused) |
Data managed | Financial, HR, operational data | Product data, design data, manufacturing data |
Primary goal | Optimize overall business efficiency | Optimize product development and lifecycle |
When to Implement ERP and/or PLM
The decision to implement ERP, PLM, or both depends on your company's specific needs and industry.
-
Implement ERP when: You need to integrate and streamline various business functions across your organization. This is a great choice for companies with complex operations or those looking to improve overall efficiency.
-
Implement PLM when: Your business involves product development, manufacturing, or engineering. It's essential for companies seeking to optimize their product development processes, improve product quality, and accelerate time-to-market.
-
Implement both ERP and PLM when: Your business needs both a comprehensive view of overall operations and a detailed focus on product development and lifecycle management. Often, these systems can be integrated to provide a seamless flow of information between departments. This scenario is common in manufacturing and engineering companies.
Conclusion: A Strategic Choice
Choosing between ERP and PLM requires a careful assessment of your company's current processes, goals, and future plans. Understanding the strengths and limitations of each system will help you make an informed decision that optimizes your business operations and drives growth. Remember to consult with industry experts to ensure a smooth implementation and maximize the return on your investment.
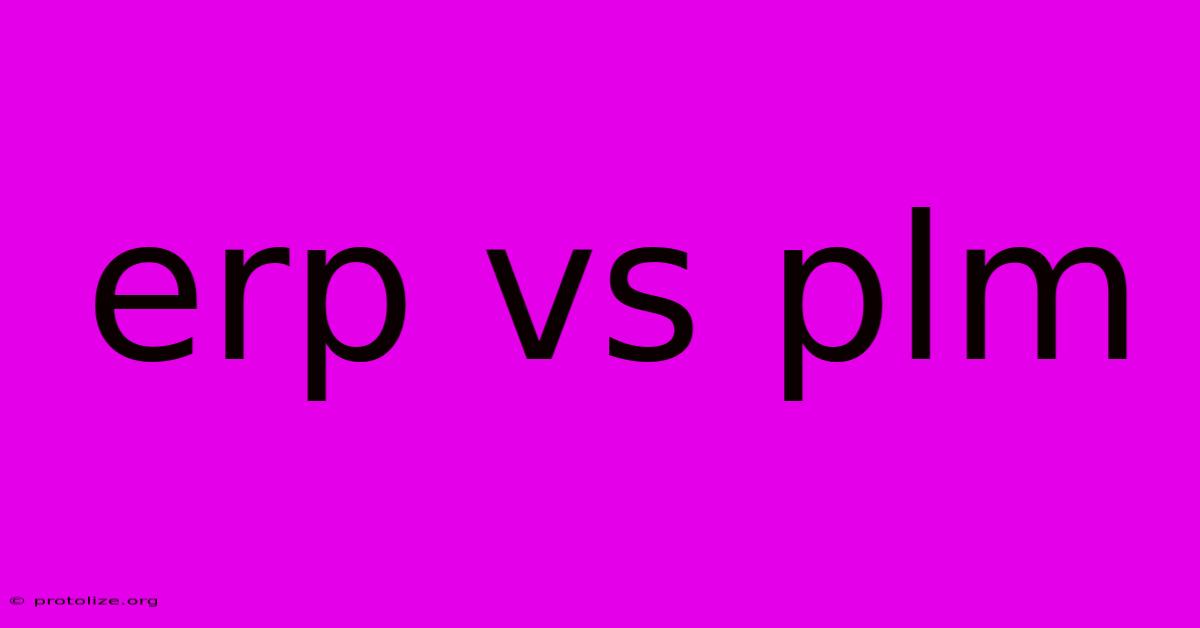
Thank you for visiting our website wich cover about Erp Vs Plm. We hope the information provided has been useful to you. Feel free to contact us if you have any questions or need further assistance. See you next time and dont miss to bookmark.
Featured Posts
-
Kupps Zero Catch Fantasy Fallout
Dec 13, 2024
-
Erp Customer Relationship Management
Dec 13, 2024
-
Astro Bot Beats Wukong Goty 2024
Dec 13, 2024
-
Erp Developers
Dec 13, 2024
-
Month Long Search Ends Hannah Kobayashi Found
Dec 13, 2024