Erp System Zerspanung
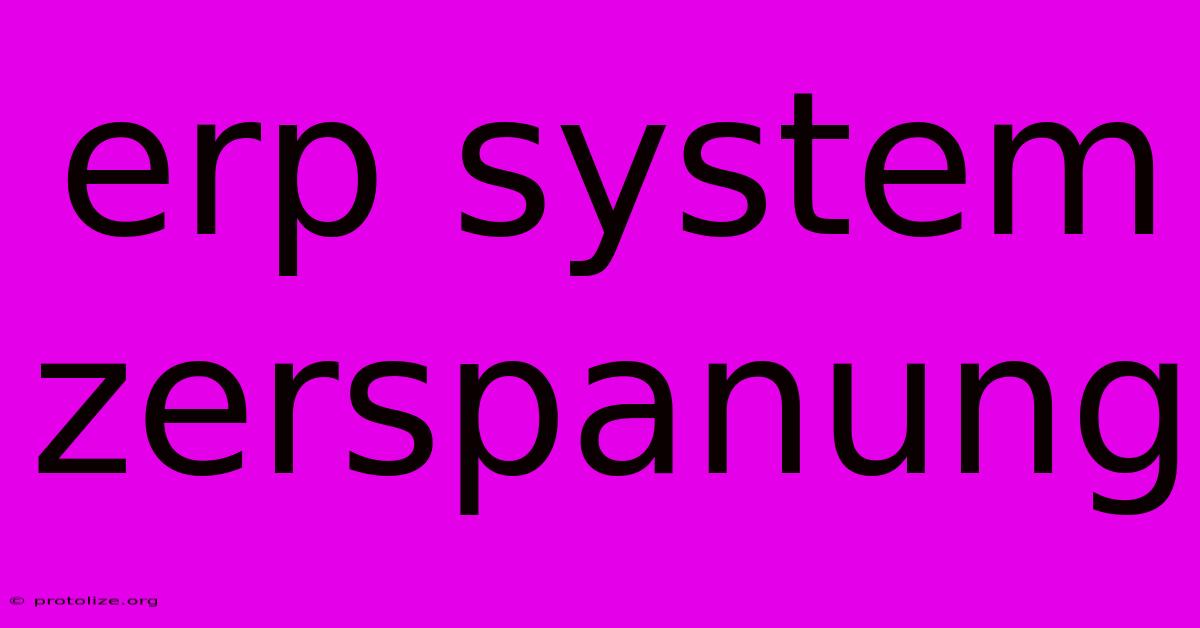
Discover more detailed and exciting information on our website. Click the link below to start your adventure: Visit Best Website mr.cleine.com. Don't miss out!
Table of Contents
ERP System Zerspanung: Optimizing Your Machining Processes
The manufacturing industry, particularly in the field of zerspanung (machining), faces constant pressure to increase efficiency, reduce costs, and improve product quality. An effective Enterprise Resource Planning (ERP) system is no longer a luxury but a necessity for staying competitive. This article explores how an ERP system zerspanung can revolutionize your machining processes.
Understanding the Challenges in Zerspanung
Modern zerspanung operations encounter numerous challenges:
- Inventory Management: Precisely tracking raw materials, work-in-progress (WIP), and finished goods is critical. Inefficient inventory management leads to stockouts, excess inventory costs, and production delays.
- Production Planning: Scheduling complex machining processes, considering machine capacity, tool availability, and skilled labor, can be a logistical nightmare. Unoptimized schedules result in bottlenecks and missed deadlines.
- Quality Control: Ensuring consistent product quality across all batches is paramount. Manual tracking of quality parameters is prone to errors and makes identifying the root cause of defects difficult.
- Cost Control: Accurate cost accounting for each job, including material costs, labor, and machine time, is crucial for profitability. A lack of transparency can lead to unexpected expenses and reduced margins.
- Data Silos: Information scattered across different departments (production, purchasing, sales) hinders efficient collaboration and decision-making.
How an ERP System Solves Zerspanung Challenges
An integrated ERP system zerspanung offers a comprehensive solution to these problems:
1. Streamlined Inventory Management
- Real-time tracking: Provides a clear, real-time overview of your entire inventory, minimizing stockouts and reducing waste.
- Automated ordering: Triggers automated purchase orders based on pre-defined parameters, ensuring timely procurement of raw materials.
- Lot and batch tracking: Facilitates traceability throughout the entire production process, essential for quality control and recall management.
2. Optimized Production Planning
- Capacity planning: Analyzes machine capacity and workload, optimizing schedules to maximize productivity and minimize lead times.
- Material requirements planning (MRP): Automatically calculates the required quantities of raw materials and components based on production schedules.
- Shop floor control: Provides real-time monitoring of production progress, enabling proactive intervention in case of delays or disruptions.
3. Enhanced Quality Control
- Automated data collection: Captures quality parameters directly from machines and sensors, eliminating manual data entry errors.
- Statistical process control (SPC): Identifies potential quality issues early on, preventing defects and reducing scrap rates.
- Traceability: Enables quick identification of the source of defects and facilitates corrective actions.
4. Precise Cost Control
- Detailed cost accounting: Provides accurate cost information for each job, including material costs, labor, and machine time.
- Performance analysis: Identifies areas for cost optimization and improves overall profitability.
- Budgeting and forecasting: Supports informed decision-making through accurate financial planning.
5. Improved Collaboration and Data Visibility
- Centralized database: Provides a single source of truth for all relevant data, eliminating data silos and improving information flow across departments.
- Real-time dashboards: Offer a clear and concise overview of key performance indicators (KPIs), facilitating data-driven decision-making.
- Enhanced communication: Streamlines communication between different departments, fostering collaboration and improving efficiency.
Selecting the Right ERP System for Your Zerspanung Business
Choosing the right ERP system is crucial. Consider factors such as:
- Industry-specific functionality: Ensure the system caters to the specific needs of zerspanung operations.
- Scalability: Select a system that can adapt to your business growth.
- Integration capabilities: Ensure seamless integration with existing systems (e.g., CAD/CAM software, CNC machines).
- Support and training: Choose a vendor that provides adequate support and training to your team.
Implementing an ERP system zerspanung is an investment that pays off in the long run. By streamlining operations, improving efficiency, and enhancing quality, you'll gain a significant competitive advantage in the demanding world of machining. The improved data visibility and analytical capabilities will empower you to make smarter, data-driven decisions, leading to greater profitability and sustained success.
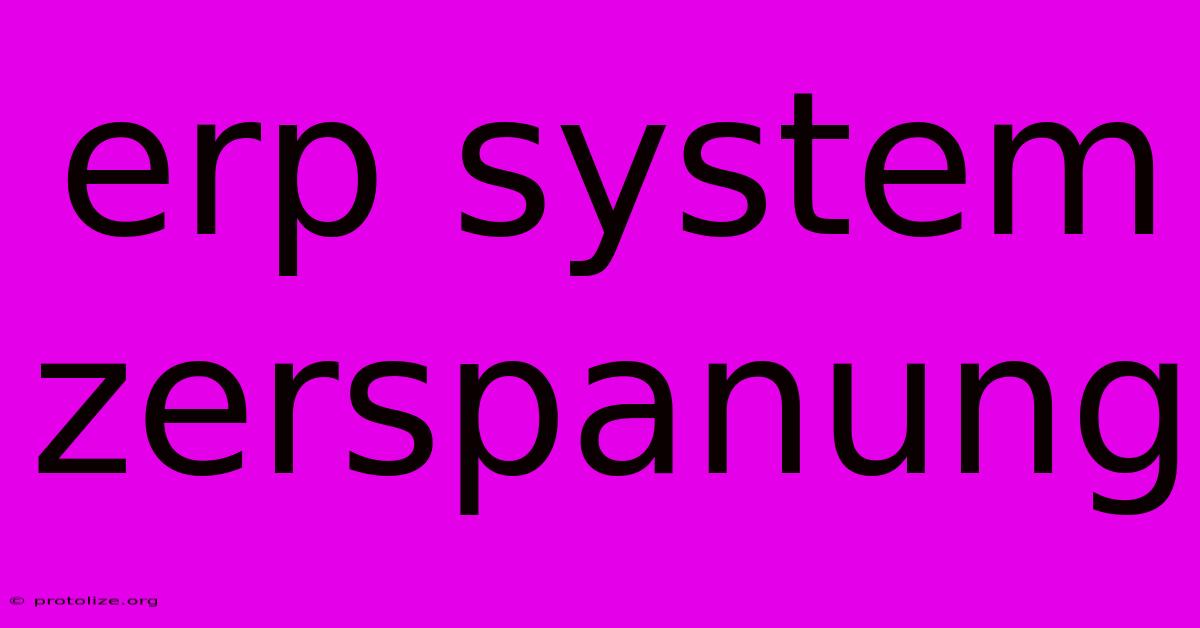
Thank you for visiting our website wich cover about Erp System Zerspanung. We hope the information provided has been useful to you. Feel free to contact us if you have any questions or need further assistance. See you next time and dont miss to bookmark.
Featured Posts
-
Citys Champions League Loss At Juventus
Dec 13, 2024
-
Citys Defeat Guardiola Questioning Tactics
Dec 13, 2024
-
Guerendo In 49ers Rams Game
Dec 13, 2024
-
Time Magazines 2016 Person Trump
Dec 13, 2024
-
Gemini 2 0 Googles Enhanced Ai
Dec 13, 2024