Erp Average Cost
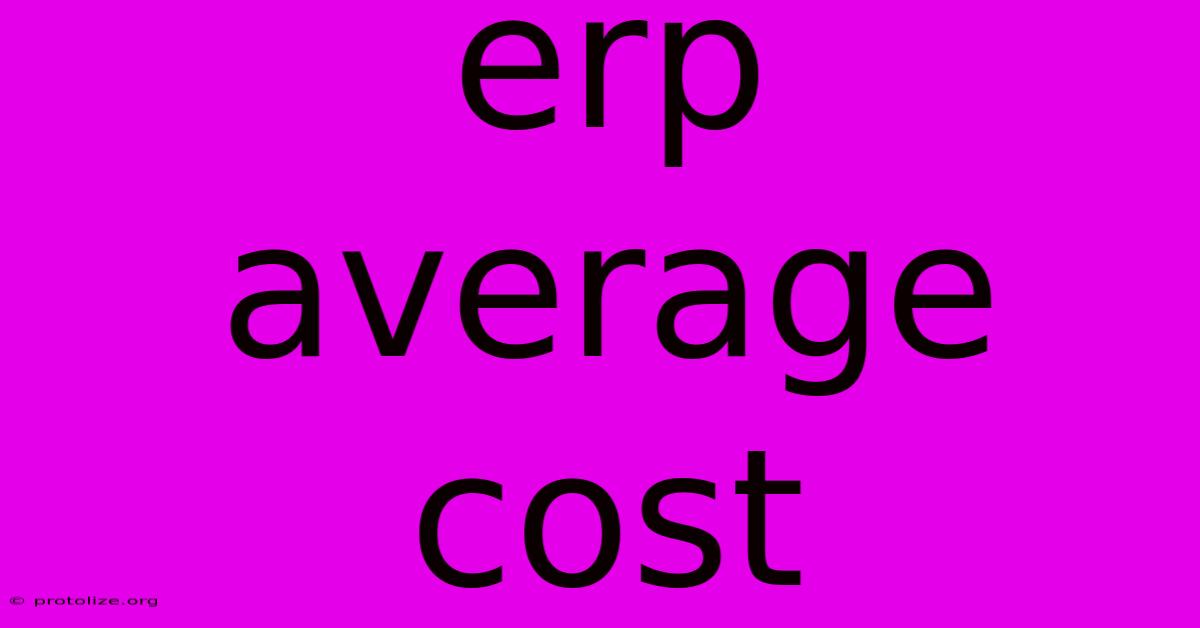
Discover more detailed and exciting information on our website. Click the link below to start your adventure: Visit Best Website mr.cleine.com. Don't miss out!
Table of Contents
Understanding and Implementing ERP Average Costing
Enterprise Resource Planning (ERP) systems are the backbone of modern businesses, managing everything from inventory and finances to human resources and supply chain. A crucial element within these systems is inventory costing, and a popular method is average costing. This article delves into the intricacies of ERP average cost accounting, explaining its mechanics, advantages, disadvantages, and best practices for implementation.
What is Average Costing in ERP?
Average costing, also known as weighted average cost, is an inventory valuation method that calculates the average cost of goods available for sale over a specific period. This average cost is then assigned to each unit sold, simplifying the accounting process compared to methods like FIFO (First-In, First-Out) or LIFO (Last-In, First-Out). Within an ERP system, this calculation is automated, providing real-time insights into inventory values.
The formula is straightforward:
Total Cost of Goods Available for Sale / Total Units Available for Sale = Average Cost per Unit
How Average Costing Works in an ERP System
An ERP system automates the average cost calculation by tracking:
- Beginning Inventory: The cost and quantity of inventory at the start of the period.
- Purchases: The cost and quantity of inventory purchased during the period.
- Sales: The quantity of inventory sold during the period.
The ERP system continuously updates the average cost per unit whenever there's a new purchase or sale. This dynamic calculation ensures that inventory valuations are always current, reflecting the latest cost trends.
Advantages of Using Average Costing in ERP
- Simplicity: Average costing is relatively easy to understand and implement, requiring less complex calculations than other methods. This simplicity reduces the risk of errors and simplifies financial reporting.
- Reduced Administrative Costs: The automation within an ERP system minimizes manual data entry and calculations, saving time and resources.
- Smoothing Out Price Fluctuations: Average costing mitigates the impact of price volatility on the cost of goods sold. This provides a more stable cost figure compared to methods that reflect immediate price changes.
- Real-time Inventory Valuation: ERP systems provide immediate access to up-to-the-minute inventory values, crucial for accurate financial reporting and decision-making.
Disadvantages of Average Costing in ERP
- Less Accurate Costing: Average costing doesn't reflect the actual cost of specific units sold, particularly in scenarios with significant price fluctuations. This can lead to less precise cost of goods sold figures.
- Potential for Misleading Inventory Values: In periods of high price volatility, the average cost may not accurately reflect the current market value of inventory.
- Not Suitable for All Industries: Average costing may not be appropriate for industries with unique, high-value items, or businesses that need precise cost tracking for each individual item.
Implementing Average Costing in Your ERP System
Successfully implementing average costing involves several key steps:
- Choosing the Right ERP System: Select an ERP system that supports average costing and integrates seamlessly with your existing business processes.
- Data Migration: Accurately transferring existing inventory data into the new ERP system is crucial for accurate calculations.
- User Training: Proper training for staff is essential to ensure they understand how to use the system effectively and interpret the data.
- Regular Monitoring and Reconciliation: Regularly review the average cost calculations and reconcile them with physical inventory counts to ensure accuracy.
- Consider Periodic vs. Perpetual Inventory: Decide whether your ERP will use periodic or perpetual inventory systemsβperpetual (continuous) inventory updates provides real-time average cost calculation.
Average Costing vs. Other Inventory Costing Methods
It's important to compare average costing with other methods like FIFO and LIFO. FIFO assigns the cost of the oldest inventory to the cost of goods sold, while LIFO uses the cost of the newest inventory. The choice of method depends on various factors, including industry, tax implications, and the need for accuracy in cost of goods sold reporting.
Conclusion: Optimizing Your Inventory Management with ERP Average Costing
Average costing within an ERP system provides a streamlined and efficient approach to inventory valuation. While it may not be ideal for every business, its simplicity, automation, and ability to provide real-time data make it a compelling option for many. By carefully considering its advantages and disadvantages and implementing it correctly, businesses can significantly improve their inventory management and financial reporting processes. Remember to choose the costing method that best aligns with your specific business needs and industry requirements.
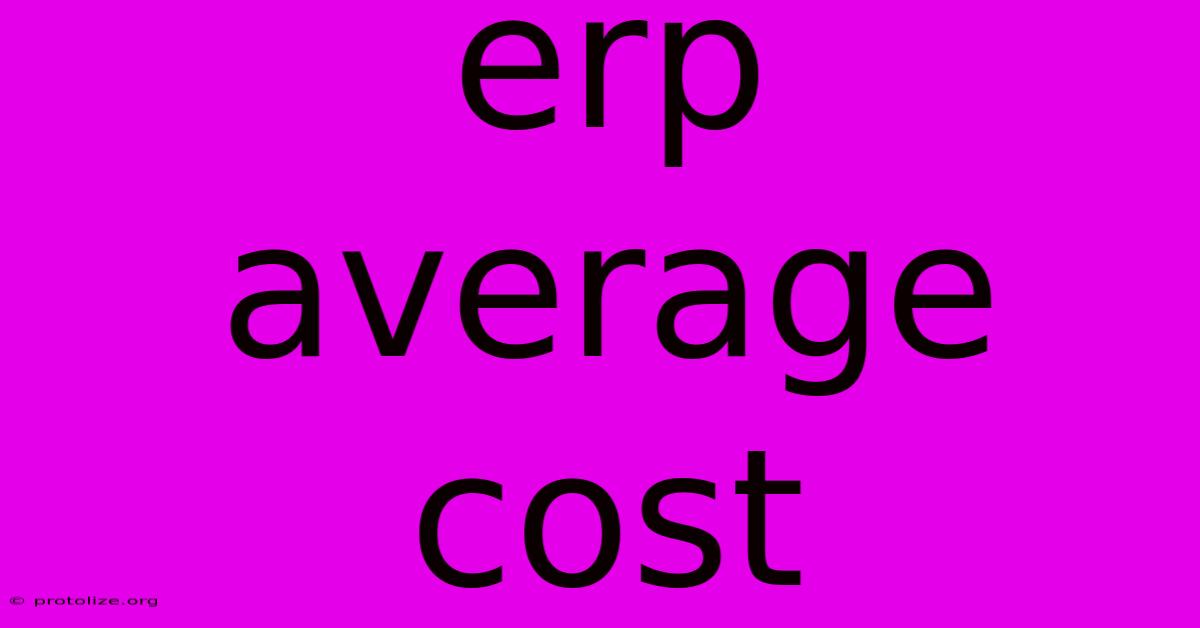
Thank you for visiting our website wich cover about Erp Average Cost. We hope the information provided has been useful to you. Feel free to contact us if you have any questions or need further assistance. See you next time and dont miss to bookmark.
Featured Posts
-
Erp Vs Erp
Dec 13, 2024
-
Paralympian Yip Pin Xiu Engaged
Dec 13, 2024
-
Le Brons Lakers Absence Personal Reasons Cited
Dec 13, 2024
-
Goa Five Russian Women Rescued From Sea
Dec 13, 2024
-
Tens Of Thousands Report Social Media Issues
Dec 13, 2024